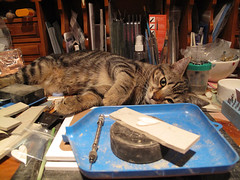
BoB the overseer
Originally uploaded by Murano Silver
BoB likes to make sure my workin's are up to standard!
Every so often his paw flicks out until I've tickled his chin enough for me to continue (BoBs quality control "wages" lol)
BoB likes to make sure my workin's are up to standard!
Every so often his paw flicks out until I've tickled his chin enough for me to continue (BoBs quality control "wages" lol)
This version shows the solder flowed on the base, then the cuff-link finding brought in ~ you'll find an alternative version on my Flickr stream showing the solder being put onto the finding and then brought onto the preheated PMC base.
(Use whichever works best for you)
Written Instructions for prep etc on on this blog post
http://pmctips.blogspot.com/2009/08/soldering-pmc-or-art-clay-silver-cuff.html
Happy making
Nic xx
p.s. The creaking noise was my chair, lol
Mini-vid tutorial on making a fingerprint charm.
Here are the Key points:
1) Make sure you have everything to cutters/rollers etc ready before your start.
2) Use thicker slats to allow enough clay for the finger to push into.
3) If the print doesn't look clean then roll it up, re-condition the clay and start again :)
4) Leave enough edge to drill a hole for the jump ring to go through.
5) Dry it thoroughly (a warm room overnight is good)
6) Sand & clean the edges (or use a baby wipe to clean up the edge if it's neat enough already)
7) For maximum strength kiln fire but if you haven't got one of those torch or hob fire in a VERY well ventilated area.
(Instructions for this are on this blog)
Happy Making
Nic xx
3rd in the series Silver Clay - the very, very basics...
How to take a good impression using a texture mat + using a cutter
Nic xx
P.S> Feel free to suggest other topics for my 60-90 second video minis :)
2nd in the series of "Silver Clay the Very Basics" this one shows you how easy it is to roll conditioned silver clay. Sorry for any clumsiness (had to use one hand so I didn't get in the way of the camera)
Nic xx
As so many people get the packet and then aren't sure what the "silver clay" should look like here's a short video of what it looks like fresh out of the packet AND how to add moisture to the clay.
If you need to re-hydrate the clay then once it's wrapped in cling film put it back in it's zip lock packet with some moistened kitchen towel. (After taking the paperwork out, lol)
Hope it's useful
Nic xx
This years conference classes included:
Jane Short ~ Basse taille brooch in a dayDorothy Cockrell ~ Cloisonne
Mr Ueedas ~ Enamel on Art Clay Silver
Jill Leventon ~ Fold Forming & Press Forming
Lesley Miller ~ Stencils for Enamelling
Janet Notman ~ Torch Firing Copper Beads
Many people were trying these things for the first time so the results are fantastic! I'm putting together some pictures on the Art Clay embellishment and enamel class I took with Toshihide Ueeda ~ it was truly a wonderful experience and he and Daisukeb Minagawa (his interpreter) made it a very pleasant learning experience.
Can't wait until the next conference!
Nic xx